Granulation in the system
Innovation of the highest quality
Our granulation lines are high-performance as well as space-saving systems for the production of pharmaceutical products. They combine the elements of the modern solid dose production line, a mixer-granulator and a fluid bed dryer with the associated sieve mills for wet and dry sieving. The two units are connected directly, so that they can be ideally fitted into the production area and the interfaces can be precisely coordinated. With our equipment, you get innovative and high-performance systems that can be adapted exactly to your requirements and conditions on site and maximise the efficiency of the process. Our many years of experience are reflected in our high-quality systems. Our granulation lines, for example, impress with their high level of operating convenience. Would you like to find out more about the advantages of our systems or do you have any questions? Contact us - we will be happy to provide you with detailed and expert advice!
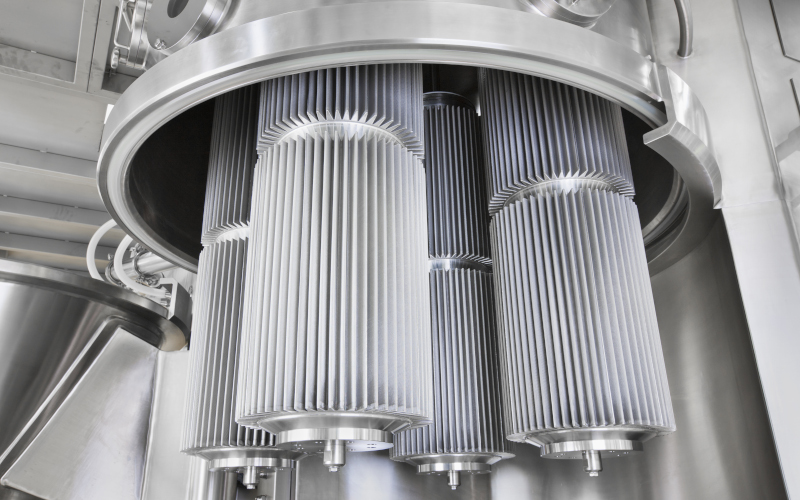
Granulating line CCS - for optimum coordination of all interfaces
This adaptability with regard to your requirements also applies to the CCS granulation line, with which moist granulation is carried out efficiently. This process, which is carried out with subsequent drying, is a reliable and efficient method by which granules are produced. The advantage of this approach is its enormous versatility, as this form of granulation can be used for most common recipes. The product flow can be realised either vertically or horizontally. In some cases, however - for example, when there are certain formulations or requirements for the structure of the end product - spray granulation in the fluid bed is sometimes necessary. But even for this case, you have a suitable solution at hand with the CCS granulation line, because the system can be prepared and retrofitted accordingly. No matter what special application you are carrying out, we will develop the right granulation process for you and find the optimum process parameters - from the clinical sample to the production batch.
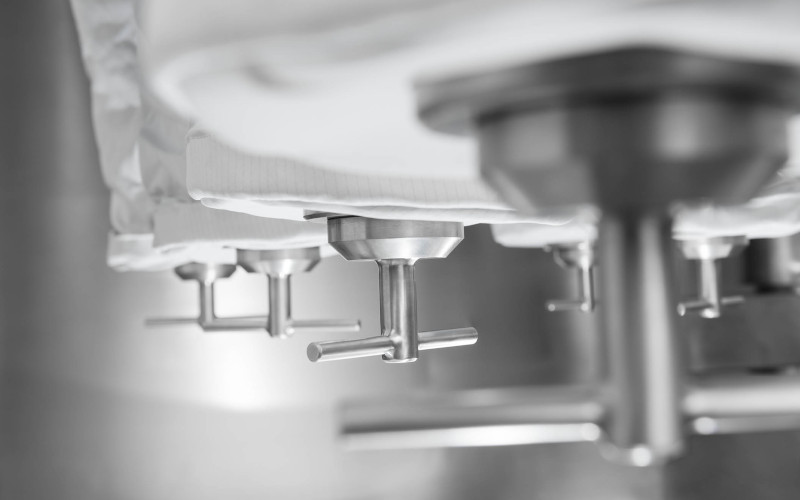
Innovative and powerful
– the CCS granulation line
Our systems for granulation score with a whole range of advantages: Thanks to reproducible processes and automated sequences with short set-up times, the system proves to be extremely efficient. Safety in the course of all work steps is guaranteed by the individual consideration of all explosion risks in accordance with ATEX and other common standards and regulations. Comprehensive cleaning concepts, ranging from WIP to CIP, ensure thorough cleaning that can be validated, and the clever through-the-wall concepts enable strict separation of production and technical areas. In the field of containment in the pharmaceutical sector, we also offer you special solutions for highly active substances. Future-oriented equipment variants and components include top spray, bottom spray and tangential spray processes in the fluid-bed dryer. Qualification is given by compliance with standards according to GAMP 5, and quality control is achieved by integrating PAT. If a space-saving and flexible pilot plant is required, the CCS-RC pelletising line is the obvious choice. Here, the plant components, the mixer-granulator and the fluid-bed dryer, can be equipped with different container sizes without tools, allowing flexible adaptation to the process.
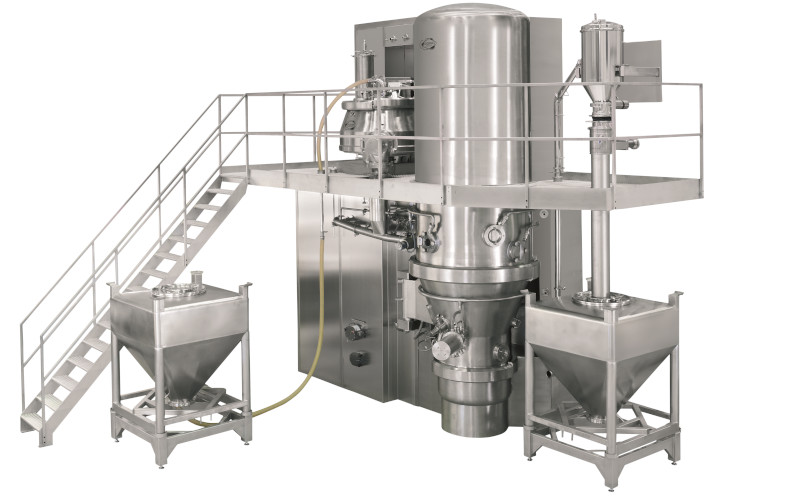
The compact and efficient
granulation line: CGS
The concept of the CGS plant integrates the processes of mixing, granulating and drying within one system on a production scale for batches from 25 to 600 kg. Here, the advantages of the CCS series are combined with additional positive features such as a small footprint as well as increased productivity and improved product yield. In addition, the installation effort for the compact unit is exceptionally low. A stable frame construction supports the mixer and the dryer. In this way, additional assembly scaffolding is not necessary. The operating media are supplied through the wall to the technical zone. Thanks to its compact design, the CGS system also requires only a small footprint and can be easily integrated into almost any space.
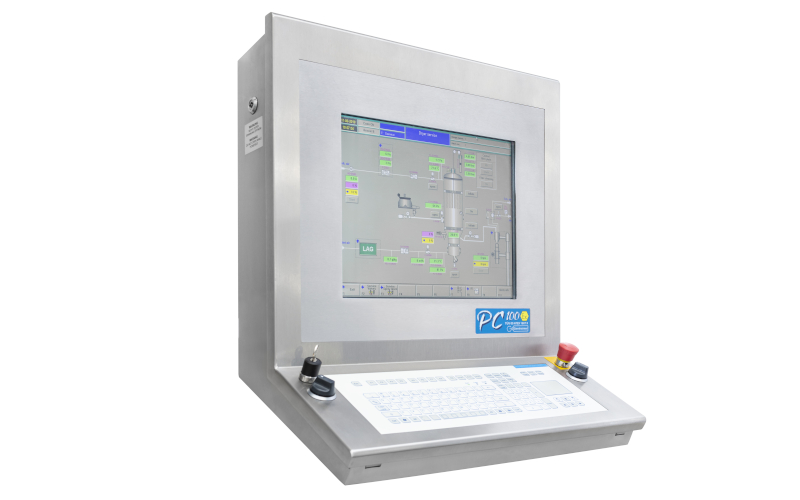
Easy and safe handling
One of the key quality features of the CCS granulation line is the control system, which was developed in-house on the basis of recognised standard systems. Intuitive user guidance and recipe creation via the phase concept create the right conditions for simple and convenient operation of the system. Extensive batch data acquisition and documentation is provided by the 21-CFR-Part-11-compliant software. You can operate both systems of the plant via a common interface, yet each of the two plant sections can be handled independently of the other. This also offers simplified conditions for maintenance and cleaning. The latter is done by using common facilities for cleaning the units.
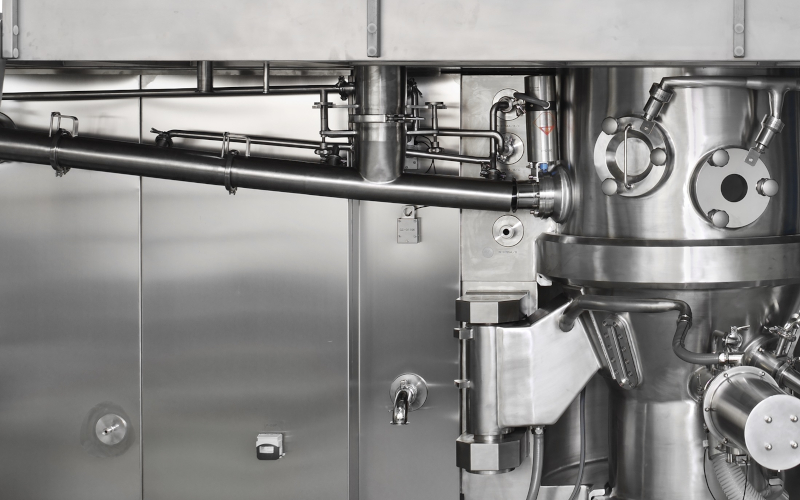
Avoiding product losses
– with the CGS system
The connection of mixer and dryer is ensured by a short and geometrically optimised line. This creates a closed transfer and a short connecting line. In this way, the transfer of the product takes place with little time and almost no residue. This short transfer time reduces product losses to an absolute minimum. Other advantages are the innovative design of the mixing tools and the tight tolerances, so that granulation takes place efficiently and maximum yield is possible.
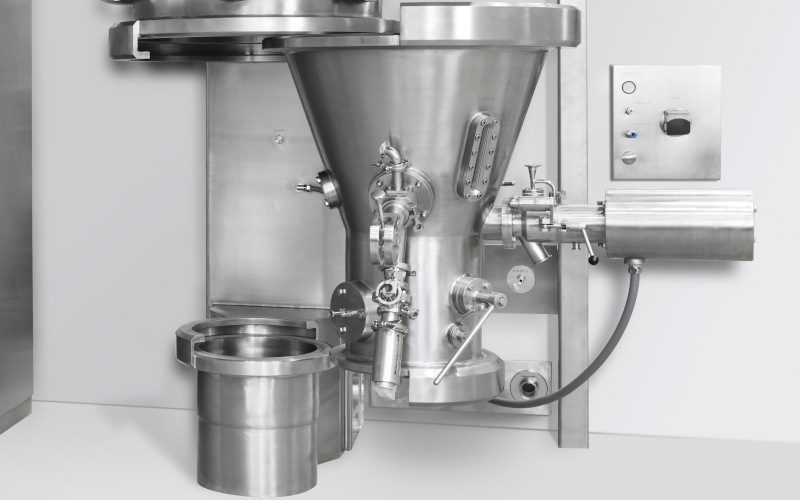
Wet granulation and drying
in one user-friendly system
In addition to high flexibility and enormous efficiency, the CGS systems offer an increased level of safety, as they have integrated explosion protection for solvent applications. This not only increases safety during production, but also reduces costs, set-up times and handling effort. The operation of the units is uncomplicated, as there is easy access to all components. Normally peripheral equipment has been integrated into the system in a way that allows easy access for cleaning, maintenance or inspection. Cleaning is automated for all components. The CGS systems are ideally suited for large-volume production and containment applications, as a large number of process steps take place in an enclosed area. The integration of PAT concepts is also feasible if required.